IFR plain blackout curtain fabric stands out as a marvel of engineering, blending permanent flame retardancy with over 85% light-blocking efficiency. But behind its sleek appearance lies a world of microscopic innovation and process mastery. From the challenges of piece dyeing to the secrets of fiber architecture, every detail determines how well this fabric balances safety, aesthetics, and durability.
Piece Dyeing: Where Color Meets Technical Limits
When it comes to dyeing IFR blackout fabric , conventional methods hit a wall. The phosphorus-based flame retardants embedded in the polyester yarns resist dye absorption, demanding specialized high-temperature, high-pressure (HTHP) dyeing at 130°C+. Yet heat can destabilize the flame-retardant chemistry—a problem solved by engineers through gradient temperature programming. By slowly ramping up heat, they minimize thermal stress, allowing dyes and retardants to coexist peacefully. Even the choice of dyes is a science: molecular size and polarity are fine-tuned to avoid displacing flame retardants in the fiber matrix. This precision ensures IFR plain blackout curtain fabric emerges vibrant yet retains its fire-resistant core, wash after wash.
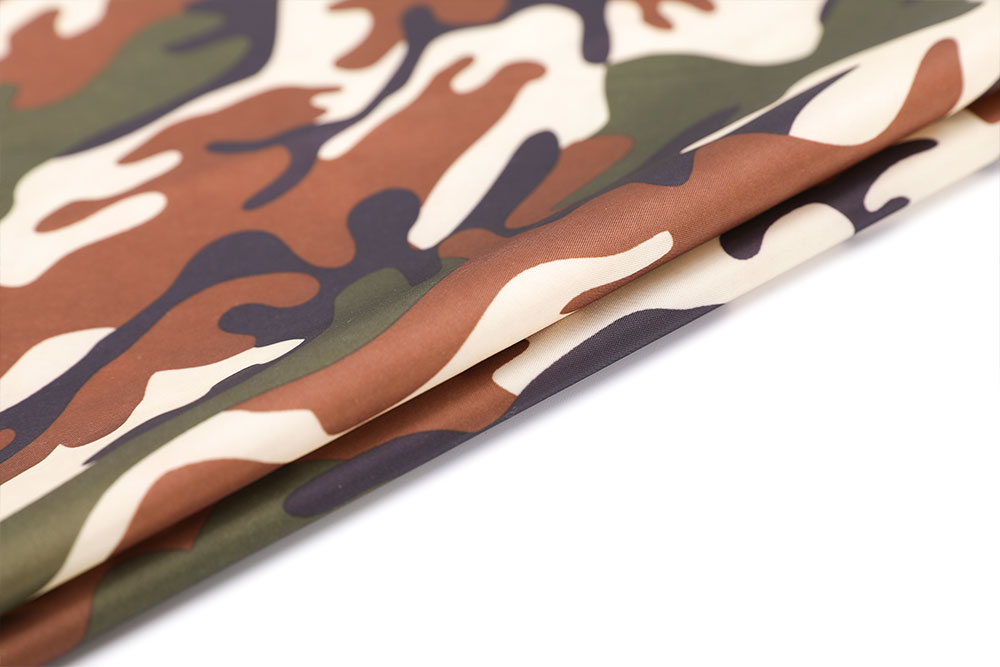
Fiber Architecture: The ‘Soft Shell, Tough Core’ Design
Zoom into the fiber’s microstructure, and you’ll find a meticulously engineered “core-sheath” system. The outer layer—a low-crystallinity polyester—delivers a soft, cotton-like handfeel, while the inner core uses high-tenacity, highly crystalline filaments for tear resistance. Flame retardants aren’t evenly distributed here; instead, they’re concentrated in the core, creating a “firewall” that resists leaching during washing. This gradient design keeps 95% of flame-retardant efficacy intact even after 50 wash cycles, far exceeding industry norms. Such structural ingenuity allows the fabric to drape elegantly while shielding spaces from light and flames.
From Lab to Living Room: Bridging Technology and Experience
What users touch in IFR plain blackout curtain fabric is more than a textile—it’s a symphony of invisible innovations. Nanoscale dye dispersion tech ensures deep color saturation without stiffening the fabric, while a matte finish on the fiber surface eliminates glare, a common flaw in lesser blackout materials. These nuances make it equally suited for hotel conference rooms and cozy bedrooms. The 280cm width? That’s no accident—it’s engineered to minimize seams in large installations, preserving both aesthetics and functionality.
In essence, IFR blackout fabric isn’t just a product; it’s a testament to how microscale engineering solves macro-scale challenges. Next time you draw such a curtain, remember: every thread holds a story of science, sweat, and a touch of invisible magic.